Untangling the Mystery of Porosity in Welding: Tips for Lessening Problems and Making The Most Of Quality
In the elaborate world of welding, porosity remains a relentless challenge that can considerably affect the high quality and integrity of bonded joints. Understanding the elements that add to porosity development is important in the pursuit of perfect welds. By untangling the enigma of porosity and executing effective strategies for flaw reduction, welders can elevate the criteria of their work to achieve premium high quality end results. As we look into the depths of porosity in welding, revealing the keys to its prevention and control will certainly be extremely important for professionals looking for to master the art of high-quality weldments.
Comprehending Porosity in Welding
Porosity in welding, an usual issue run into by welders, describes the existence of gas pockets or voids in the bonded product, which can compromise the honesty and top quality of the weld. These gas pockets are normally entraped during the welding procedure because of different elements such as incorrect shielding gas, infected base products, or inaccurate welding criteria. The formation of porosity can damage the weld, making it susceptible to breaking and rust, inevitably bring about structural failures.
By recognizing the value of preserving proper gas shielding, ensuring the cleanliness of base products, and maximizing welding settings, welders can substantially reduce the chance of porosity formation. Generally, an extensive understanding of porosity in welding is essential for welders to create top quality and long lasting welds.
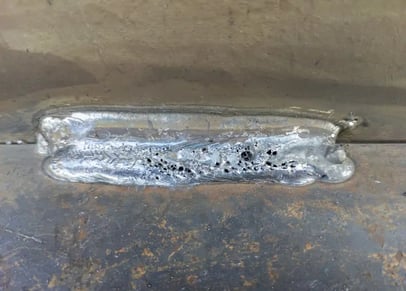
Usual Root Causes Of Porosity
When evaluating welding procedures for possible top quality problems, comprehending the typical causes of porosity is necessary for keeping weld stability and stopping architectural failings. Porosity, defined by the existence of cavities or voids in the weld metal, can substantially endanger the mechanical properties of a welded joint.
Additionally, welding at inappropriate criteria, such as excessively high traveling speeds or currents, can produce too much disturbance in the weld swimming pool, trapping gases and causing porosity. By attending to these common causes with correct gas protecting, material preparation, and adherence to optimal welding criteria, welders can decrease porosity and improve the high quality of their welds.
Methods for Porosity Prevention
Carrying out reliable preventive measures is crucial in reducing the incident of porosity in welding procedures. One strategy for porosity prevention is making sure proper cleansing of the base metal prior to welding. Impurities such as oil, grease, corrosion, and paint can cause porosity, so complete cleaning using suitable solvents or mechanical methods is vital.

Making use of high-grade filler materials and securing gases that are appropriate for the base steel and welding process can substantially minimize the risk of porosity. Additionally, preserving proper welding specifications, such as voltage, present, travel speed, and gas flow rate, is vital for porosity avoidance.
Furthermore, employing appropriate welding techniques, such as preserving a constant traveling speed, electrode angle, and arc length, can help stop porosity (What is Porosity). Ample training of welders to ensure they follow finest methods and top quality control procedures is likewise important in minimizing porosity problems in welding
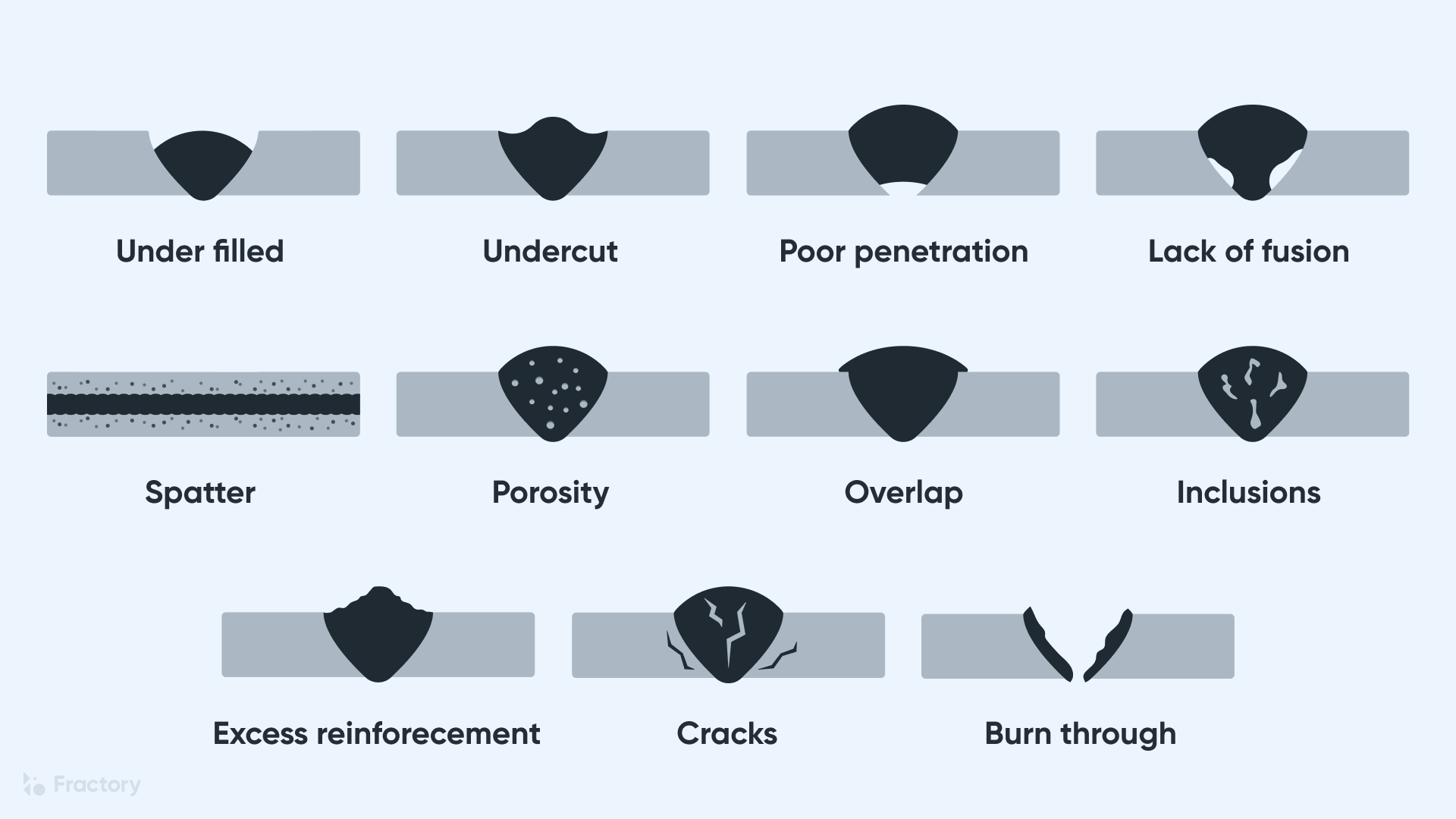
Ideal Practices for Top Quality Welds
Making about his sure adherence to market requirements and correct weld joint preparation are essential aspects of achieving regularly top quality welds. In addition to these fundamental actions, there are numerous finest techniques that welders can execute to further improve the top quality of their welds. One trick practice is maintaining appropriate sanitation in the welding area. Impurities such as oil, oil, rust, and paint can detrimentally affect the quality of the weld, causing problems. Thoroughly cleaning the workpiece and surrounding location prior to welding can help mitigate these problems.
Another best technique is to meticulously choose the proper welding criteria for the details materials being signed up with. This includes setting the proper voltage, current, travel rate, and protecting gas flow rate. Appropriate parameter selection makes sure optimum weld infiltration, blend, and total top quality. In addition, making use of premium welding consumables, such as electrodes and filler steels, can significantly influence the final weld quality. Buying premium consumables can cause stronger, a lot more durable welds with fewer problems. By complying with these ideal techniques, welders can consistently produce premium welds that satisfy sector standards and exceed client expectations.
Value of Porosity Control
Porosity control plays a vital function in making sure the stability and high quality of welding joints. Porosity, defined by click for more info the existence of cavities or voids within the weld steel, can substantially jeopardize the mechanical buildings and architectural stability of the weld. Excessive porosity damages the weld, making it extra at risk to breaking, corrosion, and total failing under functional tons.
Reliable porosity control is necessary for maintaining the wanted mechanical homes, such as toughness, ductility, and strength, of the bonded joint. What is Porosity. By decreasing porosity, welders can improve the total high quality and integrity of the weld, guaranteeing that it fulfills the performance demands of the desired application
Additionally, porosity control is essential for achieving the desired visual appearance of the weld. Too much porosity not only deteriorates the weld yet also interferes with its aesthetic allure, which can be vital in sectors where looks are important. Appropriate porosity control methods, such as making use of the correct protecting gas, managing the welding criteria, and ensuring proper tidiness of the base products, are essential for creating top notch welds with marginal issues.

Conclusion
Finally, porosity in welding is an usual issue that can endanger the top quality of the weld. By understanding the reasons for porosity and applying correct avoidance techniques, welders can minimize problems and accomplish better welds. It is necessary directory to control porosity in welding to guarantee the stability and stamina of the end product. Executing finest methods for porosity control is important for accomplishing ideal welding results.
Comments on “Recognizing What is Porosity in Welding: Causes and Solutions”